During October 2008 I helped my youngest son to acquire an embroidery factory. The guy was really excited about this and although I had my concerns about the operation I decided to support him.
Me and my partner was very busy with our own business and I could not spend as much time with WIehann as I should have and in December when I returned from Kuwait I spent some time at the Tripwired factory. The more I saw the more concerned I got and pretty soon I realised that the youngster was in over his head. I quickly concluded that with a factory like this the cornerstone of the business was the quality of the electronic files that was needed to run the machines. We bought it as a going concern from the owner who left in a hurry for Australia and I began to wonder why he was so anxious to get out of the business.
We took over all the staff and that included the factory manager who also did the digitizing. In my journey through the guts of the business I found boxes full of garments with faulty embroidery on and I rapidly came to see that the quality was way off the mark and things began to make sense to me. Being the type of guy that I am I could not really jump on the bloke about the quality because I was completely clueless about how the software worked and how the machines responded to the commands. All I knew was that they were producing crap and was loosing money hand over fist. Clients were up in arms and many orders were rejected on delivery.
So when the factory closed for Christmas I took the Software dongle and Roan installed the software for me on one of my machines here in my study/office. I have a good background with vector drawing software, Autocad, Corel Draw, 3Ds Max and Photoshop so I was quite confident that I could master the embroidery software. Well that was easier said than done. The first 4 or 5 hours was spent trying to figure out how the tools worked and how to manipulate the geometry tools. I am renowned for being a perfectionist and I spent hours and hours behind the keyboard during the following few days. By day three I was more comfortable with the software but still not nearly clued up with how the machines will respond to my creations.
Second week in January the factory opened again and I supplied the production guy with some of my creations to see the results in real life. Now here I will cut a large portion of story out ... suffice it to say that the old geezer tried everything in the book to throw me off the track and screwed up with my files in a humongous way. All the time telling me things are not right here or there and all the time being extremely vague. Well after a lot of head scratching I asked Roan to get himself up to speed with the physical operation of one of the machines so that me and him can figure the problem out with my digitizing. So it happened that on a weekend me and him sat in that factory and started working with my files. Within minutes we realised what was happening and he had to reatrain me or I would have been up for manslaughter.
Now we knew that there was not much wrong with my digitizing and between him and me we turned the screws on the production guy. Three weeks in and he just up and left.
I secured the service of a contract digitizer to assure the factory could stay up and running but at the same time I decided it was time to test my newly acquired skills. I sat down and stared at the screen for a long time and decided that for me it is better to go for broke and I placed an image of my LT on the drawing board. My son and my wife told me I was crazy to tackle such a complicated task as a test run but I know how my mind work and new that a task like this will give me immediately the pointers that I needed in order to judge myself and make a business decision. That night was hard, I knew that the whole factory depended on me and I slogged on till sunrise. By 08h00 I sent the file down to the factory and Roan called me after about two hours ...
"Damn ... it came out excellent ! You can relax ... we are back in business."
Well ... here is the result.
During the days I digitized the usual stuff for the factory and at night I indulged in my new found hobby.
I decided to do a collection of bikes because I asked around and nobody knew of any noteworthy bike embroideries around. Here are some of the bikes in my current collection.
BMW R1200GSA
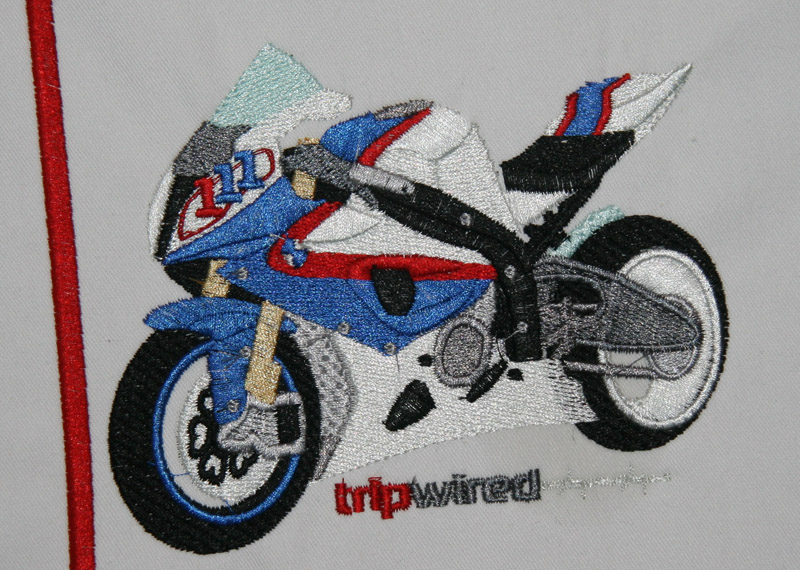
BMW S1000RR
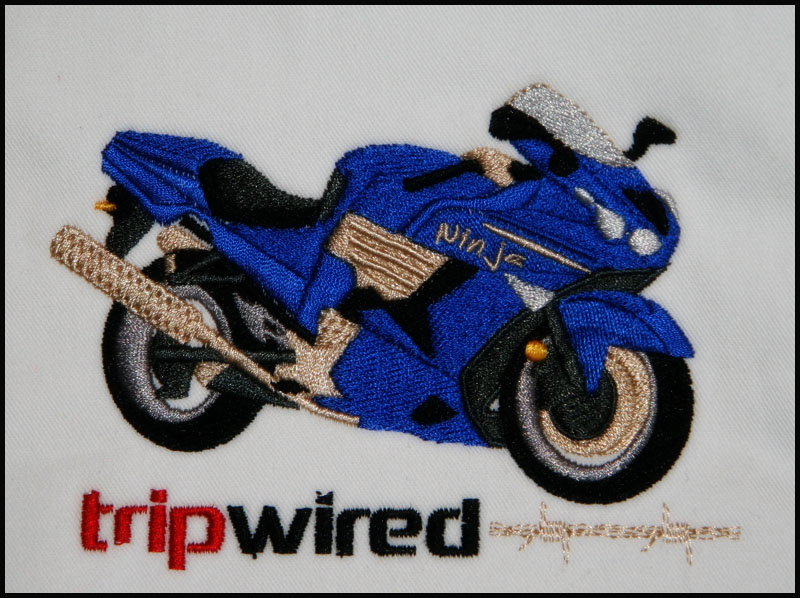
Kawasaki ZX14
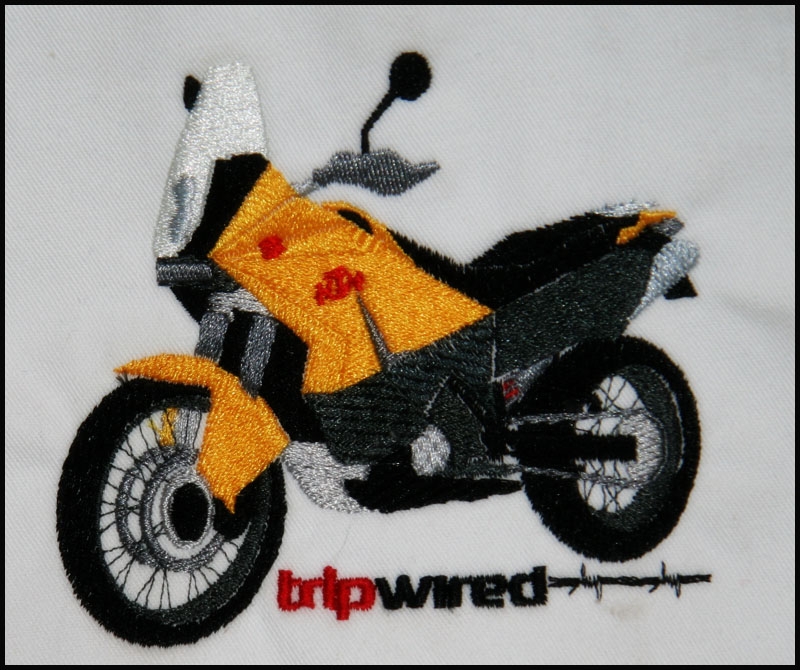
KTM 990
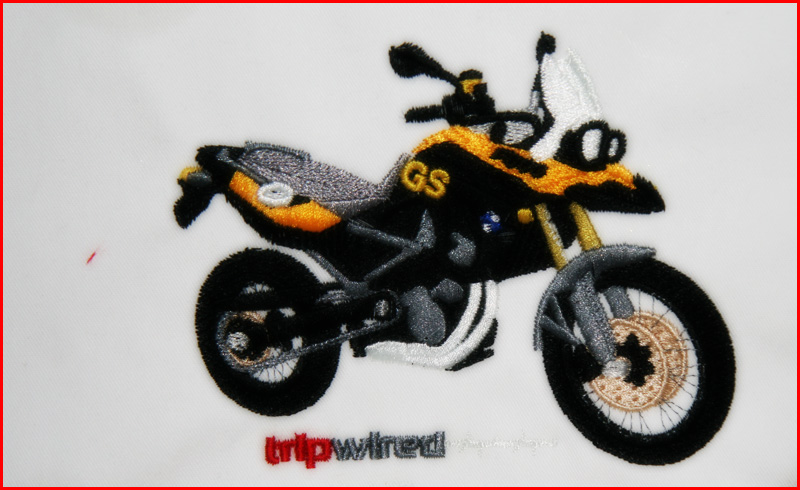
BMW F800GSThe business is now back on track and stringent quality control and complete commitment to not compromise on quality is bringing old customers back. Innovations and the willingness to push the envelope is making a name for Tripwired now. For me it is great to see the the results on the garments and I do have a sense of pride when I hear people talk about the quality. My son had to learn that you cannot be the cheapest and the best and he had to accept that you cannot get every order that is up grabs. Some clients are only concerned about the costs and those are the ones that you do not want in your portfolio.
I am now busy training a youngster to take over the production digitizing but for me the challenge and subsequent satisfaction to do complex and difficult things will keep me active on the sidelines.
This exercise has just once again confirmed my belief that we are capable of everything until we actually try and fail.
